LFAM (Large Format Additive Manufacturing) is an advanced 3D printing method that enables the production of large components exceeding the size limitations of traditional 3D printers. Unlike conventional additive techniques, which are often limited to creating small parts, LFAM focuses on manufacturing sizable objects, often measured in meters.
This technology is used across various industries such as aerospace, automotive, construction, and marine, where there is a demand for large, lightweight, and durable components.
The LFAM process is based on the principle of layer-by-layer material deposition, similar to standard 3D printing, but the key difference lies in the scale and types of materials used. The technology typically employs thermoplastic polymers and composites (e.g., materials infused with carbon fibers), which are extruded through a large nozzle mounted on a robotic arm, gantry crane, or a dedicated gantry system.
LFAM systems are equipped with advanced control software that ensures precision and repeatability, even when producing components with complex geometries. In some cases, the process is combined with finishing techniques, such as milling, to achieve smooth surfaces and accurate dimensions.
Click to download PDF version ⤓
The term LFAM began to gain widespread usage around 2014, when large-format 3D printing technology started to attract attention due to increasing interest in manufacturing large-scale components. The term was introduced to distinguish large-scale additive systems from smaller, more general-purpose 3D printers that had previously dominated the market.
With the development of technologies such as robotic-arm-based 3D printing and advanced extrusion systems, LFAM became a recognized term for methods capable of producing large structures in a cost-effective and efficient way. The emergence of this term coincided with new applications such as the production of industrial molds, automotive body parts, and construction structures, which further boosted interest in the technology.
Among the first companies to play a key role in the development and popularization of LFAM was the American firm Cincinnati Incorporated, which introduced the BAAM (Big Area Additive Manufacturing) system in 2014—considered one of the first commercial LFAM systems. BAAM gained recognition through collaboration with Oak Ridge National Laboratory, where it was used to print automotive components such as the body of the Strati car.
SINUCRAFT: sponsor of the LFAM Edition of The 3D Printing World Guide
Other significant company was the Italian WASP (World’s Advanced Saving Project), one of the first in the world to create gigantic 3D printers, revolutionizing the approach to large-format additive manufacturing. Founded in 2012 by Massimo Moretti, WASP initially focused on developing 3D printing technology for sustainable and low-cost construction.
The company made headlines in 2015 with the presentation of BigDelta, a 12-meter delta-type 3D printer capable of producing structures from locally available materials such as clay or concrete. The project aimed to enable the construction of eco-friendly homes in resource-limited areas, earning WASP international recognition. The company quickly expanded its portfolio, exploring various technologies and materials, including pellet-based printing (FGF), robotic arms, and concrete printing.
Another European company, Thermwood Corporation, also contributed to the development of LFAM by introducing LSAM (Large Scale Additive Manufacturing) systems, which combined 3D printing with CNC machining. These companies not only laid the foundations for LFAM technology but also inspired others to explore large-format additive manufacturing, contributing to the dynamic growth of this field.
FGF, Robotic Extrusion & 3DCP (3D Concrete Printing)
LFAM encompasses a variety of technological approaches, among which Fused Granulate Fabrication (FGF) and Robotic Extrusion stand out.
FGF is a technology that uses thermoplastic granules instead of traditional filament. The process involves feeding the material in the form of small pellets into an extruder, where it is melted and deposited layer by layer. Compared to filament printing, FGF offers lower operating costs—the granules are cheaper to produce and easier to store, especially for large-scale projects. Moreover, it allows for the use of a broader range of materials, including composites with glass or carbon fibers, and even recycled materials.
Robotic Extrusion, on the other hand, is a method based on the integration of additive manufacturing with robotic arms. Instead of traditional gantry or crane systems, these setups use industrial robotic arms, which offer greater freedom of movement (up to 6 axes), high precision, and the ability to operate in non-standard environments. As a result, the 3D printer can create structures with complex geometries by adjusting the nozzle position to the shape of the project, and even print “in mid-air” using temporary supports made from the same material.
Robotic arms are often equipped with interchangeable tool heads, allowing for a combination of 3D printing with other processes, such as milling or coating. One example is MX3D, a company that used Robotic Extrusion to create a steel bridge in Amsterdam. In the context of LFAM, it's also worth highlighting WASP, whose systems—like Crane WASP—combine robotic arms with concrete or granulate extruders, enabling the construction of multi-layer architectural structures several meters tall.
3DCP - concrete 3D printing, should be mentioned as one of the fastest-growing branches of LFAM. Unlike traditional construction methods based on formwork and manual pouring, this technology enables the layer-by-layer deposition of concrete based on digital 3D models, eliminating geometric limitations and significantly shortening project timelines.
The concrete 3D printing process relies on specially formulated concrete mixes with increased viscosity and rapid setting times. The material is extruded through a nozzle mounted on a gantry system, robotic arm, or mobile platform, and then precisely placed layer by layer.
The main advantage of concrete 3D printing in the LFAM context is the significant reduction in construction time and cost. Traditional formwork—often accounting for 30–60% of a building’s cost—is no longer needed, and material is applied only where necessary, minimizing waste.
In terms of materials, concrete 3D printing often uses advanced composites, such as concrete reinforced with steel, polymer, or basalt fibers, which improve tensile strength and crack resistance. Eco-friendly mixes with fly ash, slag, or recycled materials are also becoming increasingly popular, aligning with the principles of sustainable construction.
Regulatory and standardization issues remain a challenge—many countries still lack laws that permit 3D-printed concrete structures for structural applications. Nevertheless, this technology, as part of the LFAM ecosystem, is gradually gaining acceptance, supported by ongoing research into the strength and durability of printed structures.
SINUCRAFT | Proud Sponsor of LAFM Edition
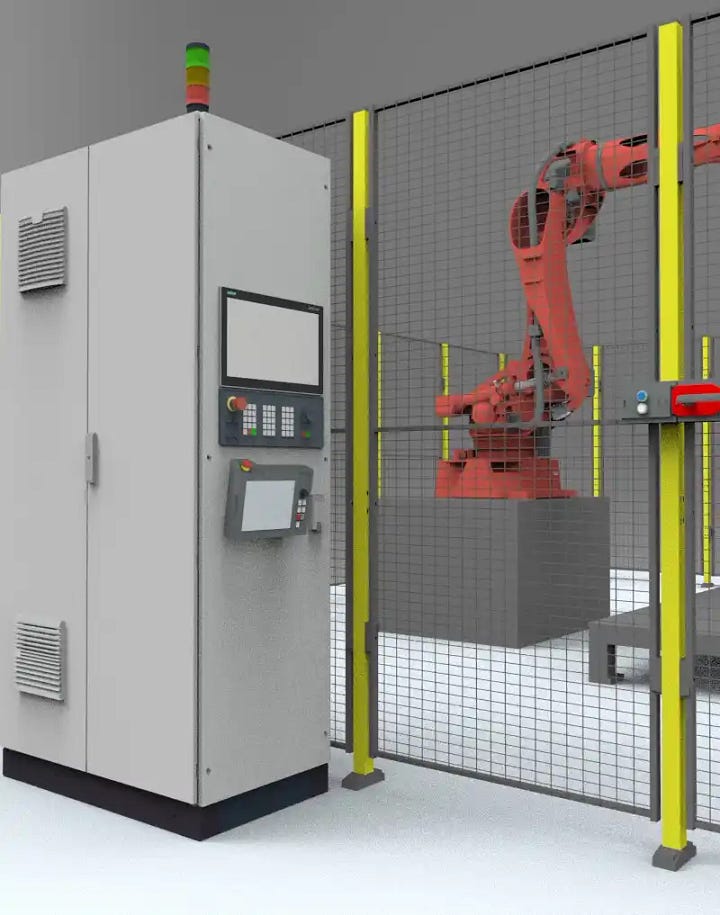

SinuCraft s.r.o.
Semtin 105, 53002 Pardubice, Czech Republic
Founded: 2024
www: sinucraft.com
e-mail: info@sinucraft.com
social media: LinkedIn
Business activities: Hardware Manufacturer
Activity: World
Overview:
Producer of CNC machines using 6 axis kinematic. Large experience in robotics and CNC controls. Each component is Europe brand with high performance.
Legacy:
20+ years of experience in robotics and CNC controls made the perfect match to design a machine for LFAM segment. Our machine can be equipped by extruder, spindle, laser cladding, MIG/MAG printer.
3DARTECH
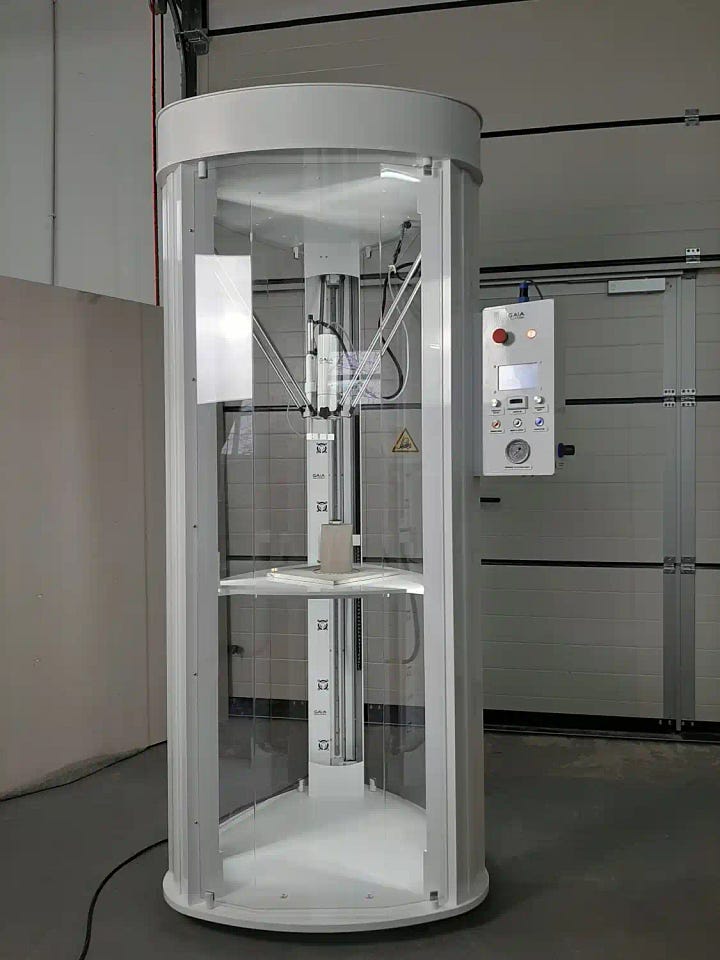
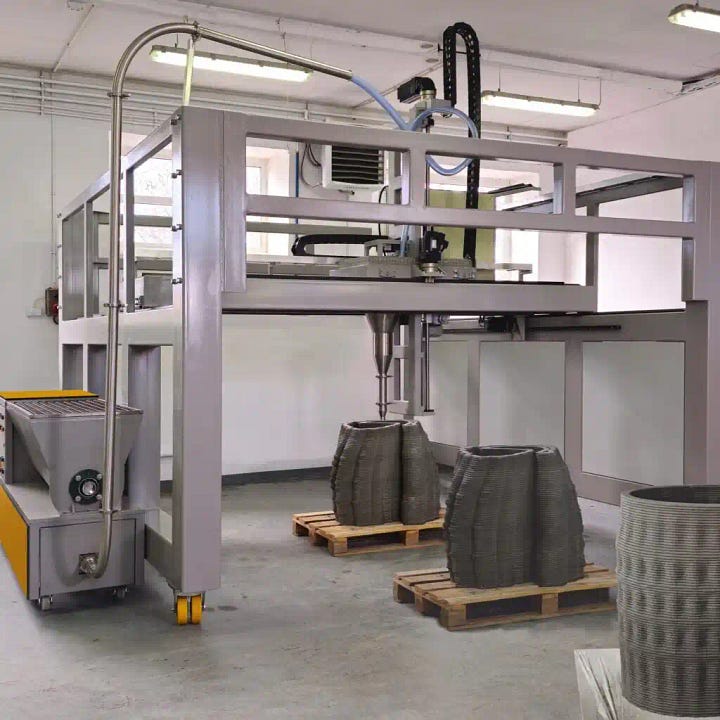
3dArtech Sp. z o.o.
ul. Malików 150D, 26-639 Kielce, Poland
Founded: 2017
www: 3dartech.com | arcusconcrete.com | gaiamultitool.com
e-mail: info@3dartech.com
social media: Facebook
Business activities: Hardware Manufacturer, Material Manufacturer
AM Services:
3DCP (Concrete 3D Printing)
Activity: World
Overview:
3dArtech is a company that specializes in the production of professional machines for 3D printing with concrete, ceramics, and facade plasters. It carries out projects and implementations at the intersection of art and mechanical engineering. The company has its own construction facilities and an art studio. Particular emphasis is placed on 3D printing of prefabricated building elements made from ceramics and concrete.
Legacy:
The company’s founders have specialized in 3D printing technology for over 15 years. 3dArtech manufactures proprietary Gaia Multitool 3D printers designed for clay printing. The company has developed its own 3D printing and modeling technology, SkribiArt, which is used in the production of facade panels and acoustic systems. It holds six patents in the field of 3D printing technology. 3dArtech has also developed and implemented a 3D concrete printing technology under the name ARCUS. Additionally, it has created its own slicer software to operate its printers.
BIGREP
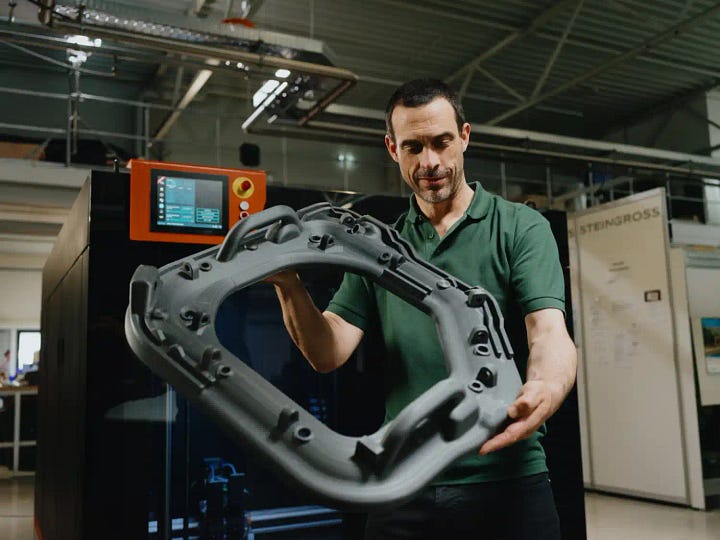
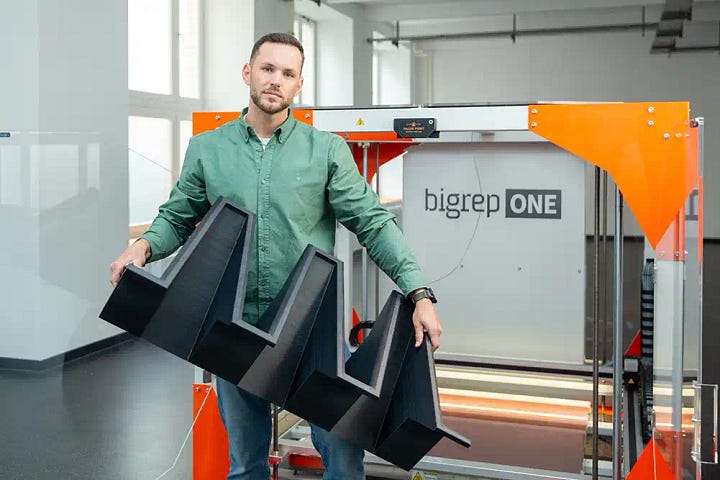
BigRep GmbH
Gneisenaustraße 66, 10961 Berlin, Germany
Founded: 2014
www: bigrep.com
e-mail: info@bigrep.com
social media: LinkedIn | Instagram | YouTube
Business activities: Hardware Manufacturer, Material Manufacturer and AM Service Provider
Activity: World
Overview:
A global leader in large-format FFF 3D printing, BigRep strives to transform its user’s productivity and creativity with easy-to-use additive manufacturing solutions. With an aim to help companies accelerate innovation and rethink manufacturing, BigRep’s German-engineered 3D printers enable engineers, designers and manufacturers from start-ups to fortune 100 companies to go from prototyping to production faster, getting their products to market first.
Through collaborations with strategic partners – including BASF, Bosch Rexroth, Etihad Airways, and Deutsche Bahn – BigRep continues to develop a complete additive manufacturing platform comprising of industrial 3D printers, software, support and advanced materials. Founded in 2014, BigRep is headquartered in Berlin with offices and technical centers in Boston and Singapore.
Legacy:
BigRep has been one of the pioneers in large-format 3D printing since it was founded in 2014 – and remains consistently focused on exactly that: industrial solutions with really large components. It all started with the BigRep One, which is now in its 5th generation. With over 1000 large-format 3D printers installed worldwide, BigRep is one of the leading providers in this segment.
At the end of 2023, the company strengthened its market position by acquiring the Austrian company Hage3D. The next major milestone followed on July 31, 2024: BigRep SE went public – a strong signal for growth and long-term ambitions.
COMPOUND DYNAMICS
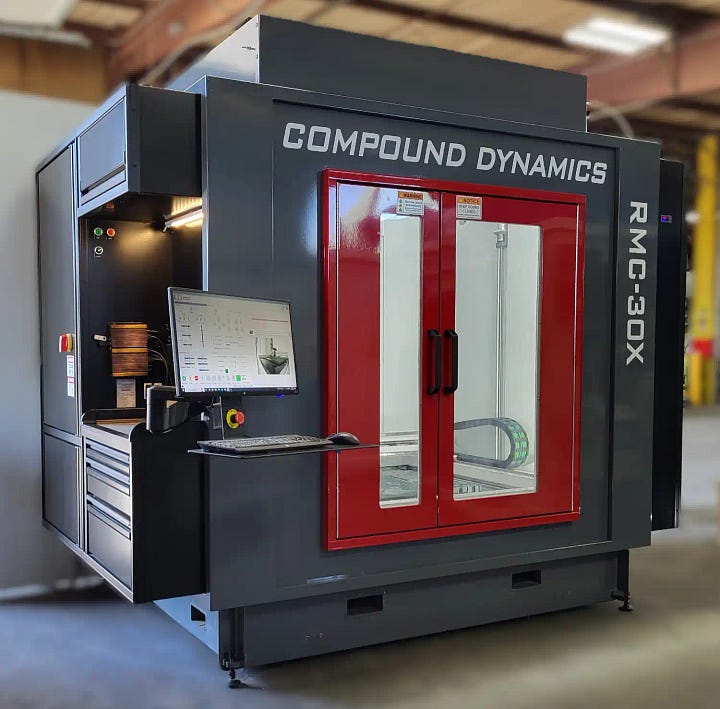
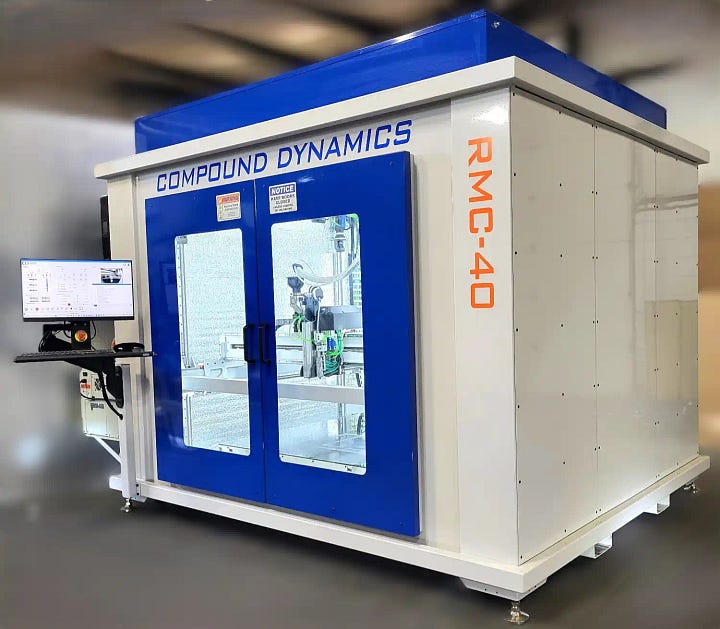
Compound Dynamics LLC
1070 Pine Street, Schofield, WI 54476, United States
Founded: 2018
www: compounddynamics.com
e-mail: jared@compounddynamics.com
social media: LinkedIn | Facebook | Instagram | YouTube
Business activities: Hardware Manufacturer and AM Service Provider
AM services:
FGF / FFF
Distribution:
RMC-40 2.25
RMC-30 1.0
Activity: North America
Overview:
Compound Dynamics LLC is an entrepreneur-led company specializing in additive manufacturing with a focus on the RM Series of 3D printers, available in two sizes and four print head configurations. These advanced machines utilize Fused Granular Fabrication (FGF) and Fused Filament Fabrication (FFF) technologies to produce high-performance, custom components with exceptional precision.
The RM Series allows for the creation of complex geometries, reducing material waste and production time. Ideal for industries like aerospace, mold-making, and education, Compound Dynamics’ machines offer versatile and scalable solutions for manufacturing durable, cost-effective parts.
Proudly American-made, the company combines state-of-the-art machine technology with custom design services to meet the unique needs of each client.
With a commitment to innovation and quality, Compound Dynamics remains at the forefront of machine-driven additive manufacturing, delivering efficient, high-quality solutions for a variety of industrial applications.
Legacy:
Founded in 2018, Compound Dynamics LLC has developed class leading technology in additive manufacturing, offering a variety of solutions tailored to applications. The company’s success is built without venture capital funding, relying instead on innovation, hard work, and customer-driven growth.
A key milestone in its journey came with its partnership with Cincinnati Inc., becoming the sole supplier of their MAAM (Medium Area Additive Manufacturing) series of printers. Known for their large-scale, high-performance capabilities, these printers allow customers to produce precision components tailored to client needs. 2024 marked the company’s best sales year to date, demonstrating the effectiveness of its machine-driven manufacturing solutions.
Proudly American-made, Compound Dynamics continues to focus on innovation, offering cost-effective, sustainable solutions while setting new industry standards for performance and efficiency in additive manufacturing.
DIVIDE BY ZERO
Divide By Zero Technologies
M–6/7 & O–1, Neighbourhood Complex, Near SBI Branch Sector 4, Palm Beach Rd, off Sarsole village, Nerul West, Navi Mumbai, Maharashtra 400706, India
Founded: 2013
www: divbyz.com
e-mail: sales@divbyz.com
social media: LinkedIn | Instagram | YouTube
Business activities: Hardware Manufacturer, Material Manufacturer and AM Service Provider
AM services:
FDM / FFF
Distribution:
Aion NX (1000 x 1000 x 1000 mm)
Aion 500 MK2
Quantum Pro 500
Activity: World
Overview:
Divide By Zero Technologies is at the forefront of industrial 3D printing innovation, setting new standards for speed, strength, and precision. Founded by Swapnil Sansare, DBZ has evolved from prototyping to manufacturing, helping global leaders like Mercedes, Samsung, Volvo, Tata Motors, and Motherson cut costs and reduce lead times.
Aion NX is a machine that knows “No Limits” with a customizable extrusion head (Palette/ Filament/ Paste/ Gel/ Hybrid) and many sensor/ automation options, having the capability to print up to 1 meter.
The Quantum Pro 500—one of the world’s fastest large-format 3D printers—prints high-strength composite parts at 500mm/s with 2.5G acceleration, challenging even CNC machining in speed and quality. DBZ’s partnership with Trinckle introduced FixtureMate—an AI-powered, no-CAD fixture design tool that enables users to design complex fixtures in under 20 minutes and print them in hours. With a growing presence in APAC and global demand from Germany, Sweden, and the USA, DBZ holds patents for high-speed printing technology and continues to lead the shift toward on-demand manufacturing.
Backed by a proven track record of profitability and execution excellence, DBZ is not just building machines—it’s redefining how the world manufactures.
Legacy:
Founded in 2013 by Swapnil Sansare to solve manufacturing challenges in India using 3D printing.
Early Days (2013–2018): Focused on FDM-based 3D printers like Accucraft and Aeqon, gaining traction with automotive giants like Mercedes and Tata Motors. Became one of India’s top industrial 3D printing companies with over 1000+ customers by 2017
Shift to Manufacturing (2018–2021): Moved from prototyping to manufacturing solutions like Go/No-Go gauges and CMM fixtures. Launched the Aion series for high-speed, composite-based production printing. Reduced lead times by 60% through partnerships with Tata Motors and Motherson Group.
Breakthrough (2022–Present): Developed the Quantum Pro 500 – 7X faster, printing at 500mm/s with 2.5G acceleration. Partnered with Trinckle to launch FixtureMate, an Cloud-based fixture design tool. Launched Quantum Pro 500 and FixtureMate at a live event in 2025 with 250+ attendees.
Now serves 1500+ clients globally, driving innovation in automotive, aerospace, and defense.
DYZE DESIGN
Dyze Design Inc.
1505 Saint-Thomas Suite 100, LeMoyne, (Montreal), Quebec, Canada
Founded: 2015
www: dyzedesign.com
e-mail: info@dyzedesign.com
social media: LinkedIn | Facebook | YouTube
Business activities: Hardware Manufacturer
AM services:
FDM / FFF
Activity: World
Overview:
Dyze Design is a global leader in advanced hardware for industrial and large-format 3D printing. Specializing in extrusion systems, motion controllers, and high-performance components, our products are engineered to meet the most demanding manufacturing needs. From high-flow & large-scale pellet extruders to state-of-the-art motion IO control solutions, Dyze Design delivers tools that enable faster, more reliable, and precise additive manufacturing processes, for real-life production applications.
Dyze Design’s offerings stand out for their robustness, ease of integration, and compatibility with challenging materials like carbon-fiber composites and engineering-grade thermoplastics. This makes the company the partner of choice for industries such as aerospace, medical, construction, and automotive.
Driven by a commitment to innovation and customer success, Dyze Design continually redefines industry standards. Its focus on R&D and user-centric design ensures our solutions empower manufacturers to scale production efficiently while maintaining exceptional quality, unlocking new possibilities in industrial-grade 3D printing.
Legacy:
Founded in 2015 in Montreal, Canada, Dyze Design has built a strong reputation for innovation and excellence in additive manufacturing since its inception. Starting as a small team of engineers, it quickly gained recognition for solving some of the industry's most complex challenges, including high-flow material extrusion for large format 3d printing and advanced motion control to unlock digital twin capabilities and provide just-in-time 3D printed parts validation and certification.
Dyze Design’s flagship products, such as the Pulsar high-flow pellet extruder and the Typhoon high-flow filament extruder, are used worldwide to produce large-scale, production parts. These technologies are celebrated for their ability to handle high-throughput production while maintaining material integrity and dimensional accuracy.
Over the years, Dyze Design has earned numerous honors, including being 2 times finalist in the prestigious TCT Awards for our Pulsar pellet extruder and later for our Pulsar Atom small scale pellet extruder. Today, our products are trusted by leading OEMs and manufacturers, demonstrating our lasting impact on the 3D printing landscape.
Dyze Design’s legacy is one of innovation, reliability, and transformative industrial solutions.
FOOTPRINT
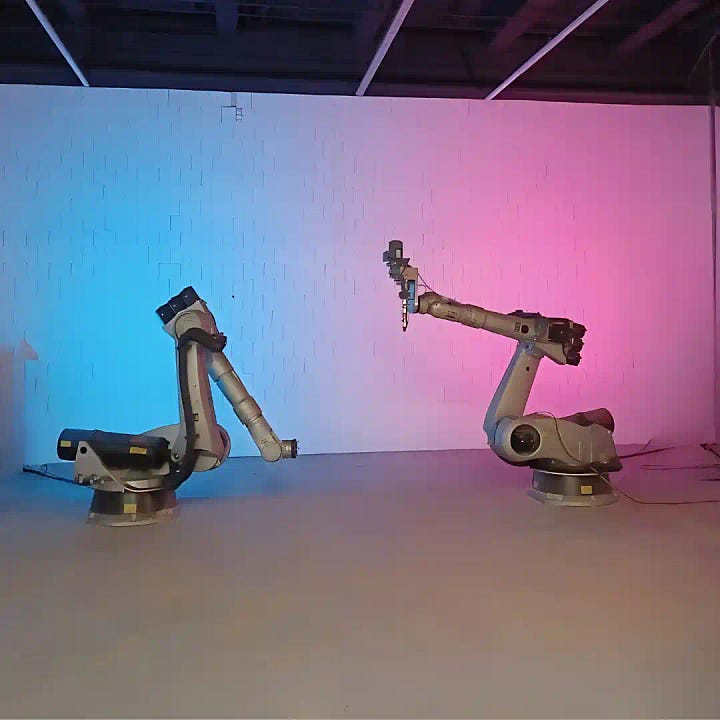
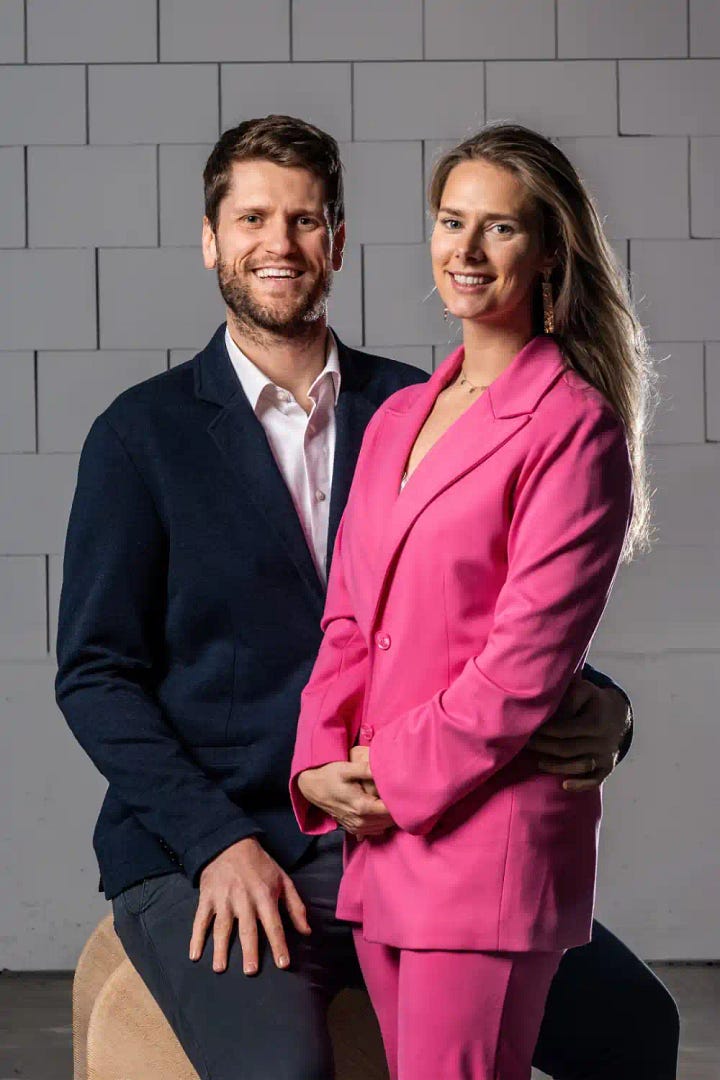
Footprint Inc.
Pathoekeweg 120G, 8000 Brugge, Belgium
Founded: 2022
www: footprintinc.be
e-mail: info@footprintinc.be
social media: LinkedIn | Instagram
Business activities: Hardware Manufacturer and AM Service Provider
AM services:
FGF / FFF
Distribution:
Footprint 3D print systems
Activity: Belgium
Overview:
Footprint Inc. makes large-scale 3D printing affordable with pellet technology.
In a market where large-scale 3D printing is often associated with high costs and complex infrastructure, Belgian-based Footprint Inc. offers a refreshing alternative. The company repurposes second-hand industrial robot arms into high-performance 3D printers equipped with pellet extruders—significantly reducing production costs compared to conventional filament-based systems.
Footprint Inc. targets companies in need of customized, low-volume production—ranging from architecture and interior design to construction, events and visual merchandising. By developing their own machines and printing directly with recycled or custom pellet blends, they offer a unique balance between scale, affordability, and design flexibility.
Every project starts with the client’s need, not with an off-the-shelf solution. This co-creative approach ensures that functionality, feasibility, and budget are always aligned. Footprint Inc. proves that innovation doesn’t have to be expensive—just smart.
Legacy:
Footprint Inc. was born from a shared passion for technology, circularity, and the power of making. Fascinated by the potential of industrial robotics and large-scale additive manufacturing, the founders saw unique opportunities in giving discarded robot arms a second life. By combining expertise in mechanical engineering with a deep-rooted belief in sustainable production, Footprint Inc. developed into a pioneering force in affordable, pellet-based 3D printing.
The company received early-stage innovation support from VLAIO (Flemish Agency for Innovation and Entrepreneurship), allowing them to scale their ambitions from a bold idea to a functional tech lab. Since then, Footprint has collaborated with the Belgian Navy on technical prototyping and has delivered bespoke work for prominent Belgian artists and designers, including Nick Ervinck and Hoet Design Studio.
What began as a side project in machine building has evolved into a full-fledged mission: making industrial-scale 3D printing accessible, functional, and future-ready.
FUSED FORM
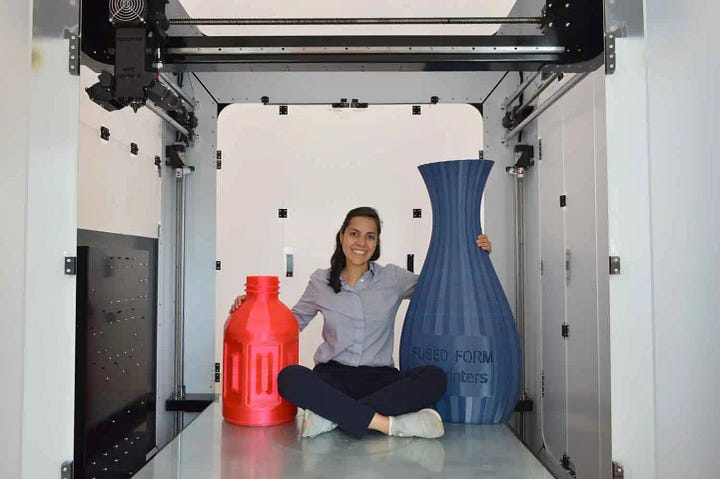
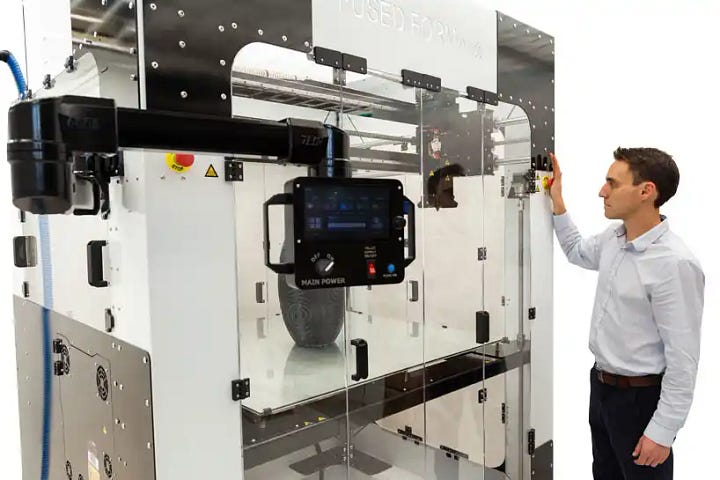
Fused Form
Km 1.4 Via Chia-Cota, Colombia
Founded: 2013
www: fusedformcorp.com
e-mail: comercial@fusedformcorp.com
social media: LinkedIn | Instagram | YouTube
Business activities: Hardware Manufacturer
AM services:
FGF / FFF
Distribution:
Fused Form P1300
Fused Form P600+
Fused Form FF600+
Fused Form FF300
Activity: World
Overview:
Fused Form is redefining industrial 3D printing with cutting-edge, pellet-based additive manufacturing. A cost-effective and sustainable alternative to filament systems is being provided by the company, enabling faster production, greater material versatility, and lower operational costs. A commitment to optimal design in mechanisms and systems is maintained by Fused Form to ensure reliability, efficiency, and top performance.
Custom 3D printers tailored to specific industrial applications are being designed and built by Fused Form. Whether unique material requirements need to be addressed, build volume increased, or specialized production processes optimized – solutions are being delivered accordingly.
A focus is placed on large-format, high-speed 3D printing for industries such as foundry, furniture, and manufacturing, where material costs are reduced and productivity is enhanced.
Key advantages are offered by Fused Form, including an optimized product for fast ROI, direct support from development engineers, and access to full product developers.
At Fused Form, smart engineering is believed in. That is why the motto “Keep it simple, high performing” is upheld.
Legacy:
With 12 years of experience as a 3D printer manufacturer, expert guidance is provided by Fused Form, along with the delivery of the latest advancements in additive manufacturing. Custom 3D printers with excellent lead times are developed through fast-paced innovation.
One of the key achievements by Fused Form includes the development of a custom 3D printer with integrated sensors, AI, and a high-speed rotational nozzle for the University of Wisconsin–Madison. This was created as a proof of concept for a patent granted to Prof. Tim A. Osswald and Dr. Allen Roman. Nozzle throughput is enhanced and anisotropy reduced by this system, demonstrating the company's ability to create high-performance, application-specific solutions.
A legacy built on innovation, precision, and adaptability is maintained by Fused Form. The technology has been successfully exported to the USA, Canada, Germany, Portugal, Italy, Switzerland, Ecuador, Chile, and Spain, expanding the company's global impact.
GINGER ADDITIVE
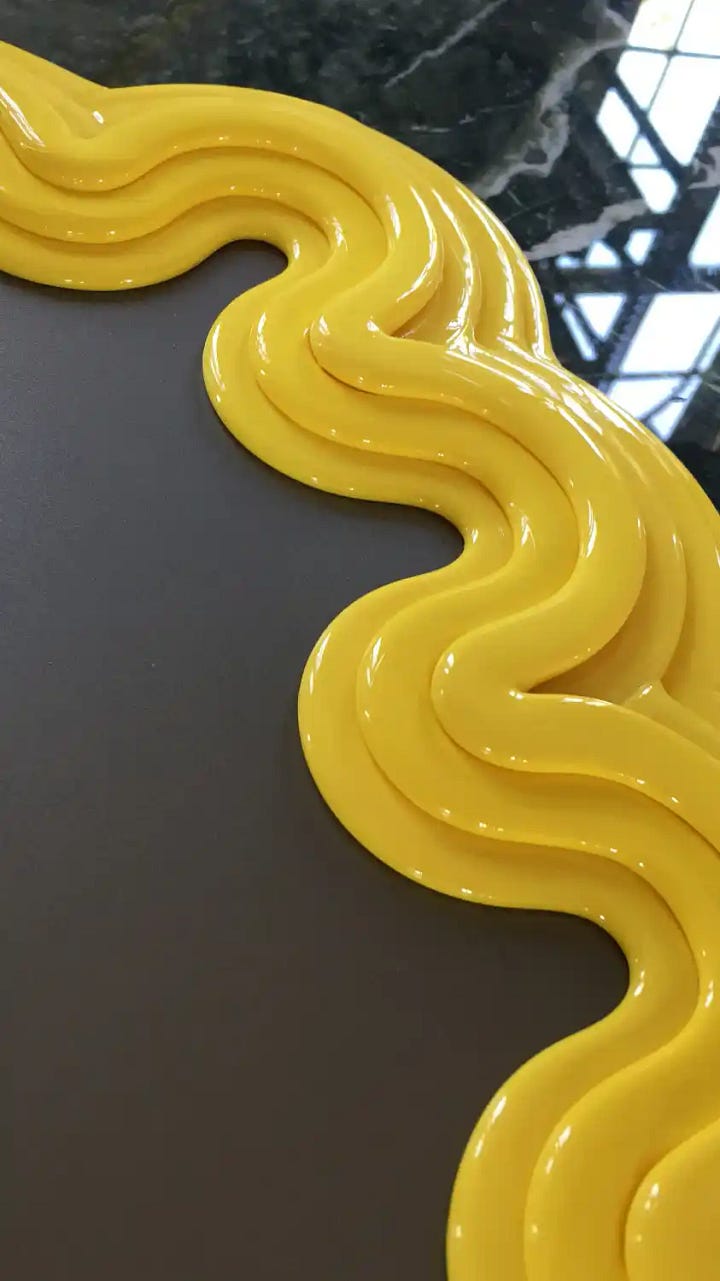
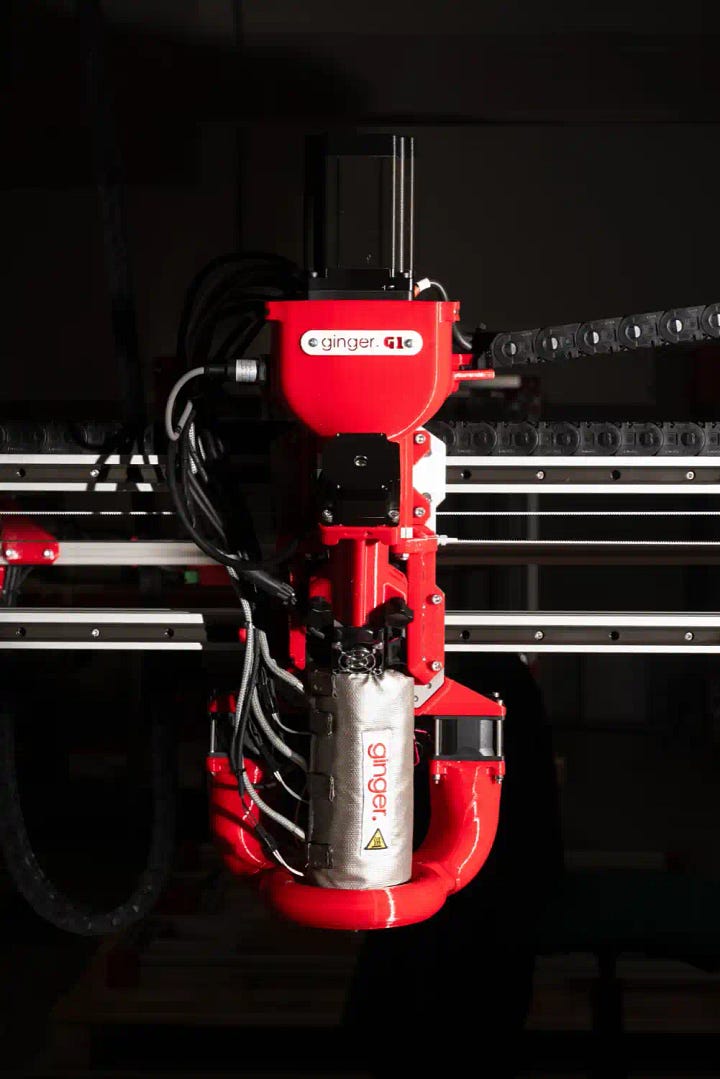
Ginger Additive slrs
Via Vittorio Veneto 44, 20093, Cologno Monzese, Milano, Italy
Founded: 2021
www: gingeradditive.com
e-mail: info@gingeradditive.com
social media: LinkedIn | Instagram
Business activities: Hardware Manufacturer
AM services:
FGF / FFF
Activity: World
Overview:
The G1 printer by Ginger Additive is designed for professional use in industrial environments. With a build volume of 1x1x1 meters, the G1 is considered ideal for large prototypes, components, and functional parts.
A high-performance extruder is used to process up to 2 kg of material per hour – including technical materials such as glass or carbon fiber-reinforced filaments. A heated bed and enclosed frame are provided to ensure optimal conditions for demanding prints.
An automatic feeding system is included to allow for uninterrupted printing. With Orca Slicer integration and Clipper firmware, high-speed, efficient performance is delivered by the G1.
Technical Highlights:
1,000 x 1,000 x 1,000 mm build volume
Up to 2 kg/h is extruded
CF/GF-reinforced materials are supported
A heated bed and enclosed chamber are included
Material is fed automatically
Orca Slicer is integrated
Clipper is used for high-speed printing
Price: €15,500
On-site setup and hands-on training workshop are included.
The G1 is considered perfect for companies relying on large-format FDM printing with a focus on reliability, speed, and material flexibility.
Legacy:
From Suburban Workshop to Global Adoption – The Story Behind the G1
Founded in 2021 by Davide Malnati and Umberto Bisotti just outside Milan, the mission of Ginger Additive was defined simply: to build the first truly affordable, large-format pellet 3D printer. What started as a bold prototype was quickly adopted by architects, designers, and creatives working at the intersection of furniture, art, and culture.
By early 2025, the G1 was launched by the Company as the first product built for mass production. Today, it is being used worldwide. Integration of the G1 into production workflows has already been carried out by several multinational companies, and seamless compatibility is being recognized with pride by Ginger Additive.
At Ginger Additive, robotic manufacturing is regarded as a cornerstone of future industry — and the future is being built one layer at a time.
GRUPA AZOTY
Grupa Azoty SA
ul. Kwiatkowskiego 8, 33-101 Tarnów, Poland
Founded: 1927 (2019 entered the AM business)
www: grupaazoty.com | nowetechnologie.grupaazoty.com
e-mail: druk3d@grupaazoty.com
social media: LinkedIn | Facebook | Instagram | TikTok | YouTube
Business activities: Material Manufacturer
AM services:
FDM / FFF
SLA / DLP
SLS
Distribution:
Tarfuse – filaments
Tarfuse – pellets
Tarfuse – liquid
Tarsint – powder
Activity: World
Overview:
Grupa Azoty has been producing materials for additive technologies for industrial applications, such as granulates, filaments, resins and powders since 2019.
Grupa Azoty has been involved in extrusion and mixing of polymers for nearly 50 years, and additive production has allowed us to expand our offer with a line of unique granulates and filaments.
The granulates we produce under the trade name: Tarfuse G PA NAT, Tarfuse G PA CF15, Tarfuse G PA GF20, Tarfuse G PETG GF30 are dedicated to industrial recipients for large-format prints. Our offer also includes prints and design materials for utility prints.
Modification of plastics, development polymer formulation and quality control.
Development of materials according to customer specifications, specialist knowledge in the field of tool materials and processes in many applications gives us a huge advantage and enables us to support each customer.
Legacy:
The Grupa Azoty Group was established in 1927. The Group is one of the leading players on the European fertilizer and chemical markets. The Group comprises a number of entities, including: Grupa Azoty S.A. (the Parent, based in Tarnów), Grupa Azoty Zakłady Azotowe Puławy S.A., Grupa Azoty Zakłady Chemiczne Police S.A., and Grupa Azoty Zakłady Azotowe Kędzierzyn S.A.
Grupa Azoty is currently the EU's number two manufacturer of nitrogen and compound fertilizers, and its other products, including melamine, caprolactam, polyamide, oxo alcohols and titanium white, enjoy an equally strong standing in the chemical sector, with a wide range of applications across various industries.
However, we recognize that the most valuable asset of Grupa Azoty is its employees. With a workforce of around 15,000, we understand that our employees are the backbone of our success. Our company's value has been built over many years by a stable shareholding structure, and we are proud to be recognized as one of the strategic companies for the Polish economy.
Certificates: ISO 9001, ISO 14001, ISO 45001, ISO 50001, IATF 16949
MASSIVIT
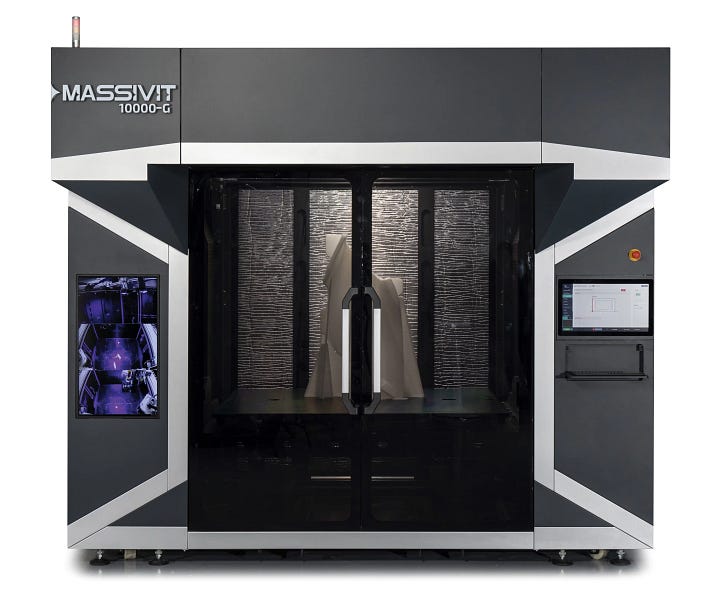
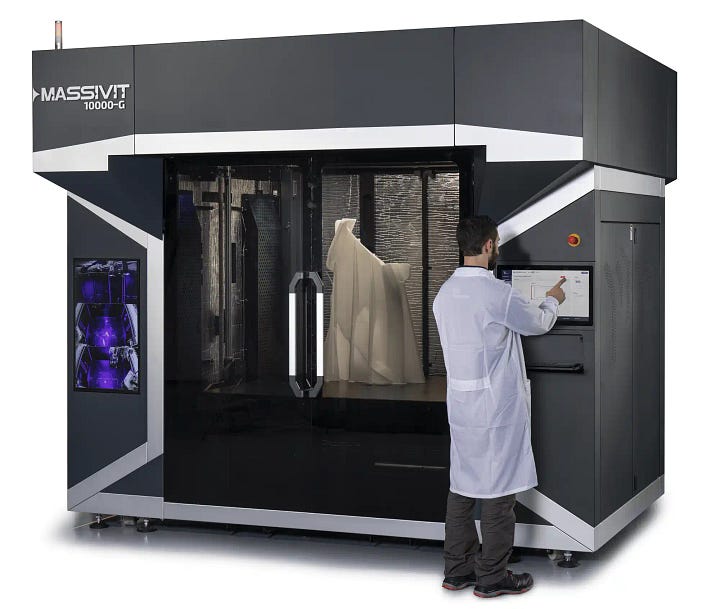
Massivit 3D Printing Technologies Ltd.
11 Lev Pesach Street, Lod, Central District, 7129361, Israel
Founded: 2013
www: massivit3d.com
e-mail: info@massivit.com
social media: LinkedIn | Facebook | Instagram | YouTube
Business activities: Hardware Manufacturer and Material Manufacturer
AM services:
GDP
CIM
Activity: World
Overview:
Massivit’s vision is to transform manufacturing of large parts from traditional processes to ultra-fast, digital fabrication using industrial-grade materials. Driven by a passion to solve real-world manufacturing needs, Massivit has developed a portfolio of large-scale 3D printers that are enabling customers across 40 countries to automate their production, reduce manufacturing costs, and minimize waste.
Massivit brings to market a portfolio of groundbreaking, large scale 3D printers that are transforming manufacturing in a range of industries including automotive, marine, rail, consumer goods, sporting goods, and scenic fabrication.
Massivit’s large format 3D printers (LFAM) are based on two innovative technologies, Gel Dispensing Printing and Cast In Motion, and are able to produce full-scale, custom production parts, industrial molds, or functional prototypes within hours.
Legacy:
Massivit 3D Printing Technologies Ltd. (Tel Aviv Stock Exchange: MSVT) is a leading provider of industrial 3D printing systems for the automotive, marine, railway, and additional markets. The company’s solutions enable cost-effective production of large parts, molds, and prototypes at unprecedented speed.
Massivit’s vision is to transform manufacturing of large parts from traditional processes to ultra-fast, digital fabrication using industrial-grade materials. The company was founded in 2013 by a team of experts led by Gershon Miller.
Its headquarters are based in Lod, Israel and the company provides its worldwide community with end-to-end services supported through an extensive dealer network.
R3DIMENSION
R3DIMENSION 3D PRINTERS, SL
Avenida Sagunto 116, nave 6, Edificio CEEI Aragón, Spain
Founded: 2022
www: r3dimension.com
e-mail: info@r3dimension.com
social media: LinkedIn
Business activities: Hardware Manufacturer
AM services:
FDM / FFF
Activity: World
Overview:
R3DIMENSION is a large format spanish FDM 3D printers manufacturer. The entire process is carried out at its facilities, from the design and development phases to the assembly and marketing of the printers.
Through the development of its own technology, it is able to offer its customers a comprehensive service in terms of additive manufacturing, ranging from feasibility studies for the integration of 3D technology, through the marketing of its printers, to providing support services in the use and operation of its machinery.
Identity model is the first FDM 3D printer developed and marketed by R3DIMENSION, professional large format 3D printer that can print on a large scale products with high quality finishes; its unique features such as the Static Printing Platform and the IDEX Printing System allow it to be the most productive on the market thanks to the possibility of simultaneous printing.
Legacy:
R3DIMENSION has managed to differentiate itself from the competition thanks to the unique features of its 3D printers, the most notable of which are:
Printing volume: 1.120 x 720 x 620 mm
Deposition rate up to 760 gr/h
IDEX printing system (double independent extrusion). Allows to double productivity by being able to print on several models: copy, mirror, multi-material
Static printing platform throughout the entire printing process, improving the quality and speed of production
Filament (material) loading capacity of up to 20 kg
Full front access, optimising space for maximum usability
Ergonomic working height, with a 95 cm platform and a 7’ touchscreen display
Power supply system, micro-cut and surge protection.
Variety of materials available: ABS, ASA, FLEX, HIPS, PETG, PLA, PCCF, PACF.
TRIDEO
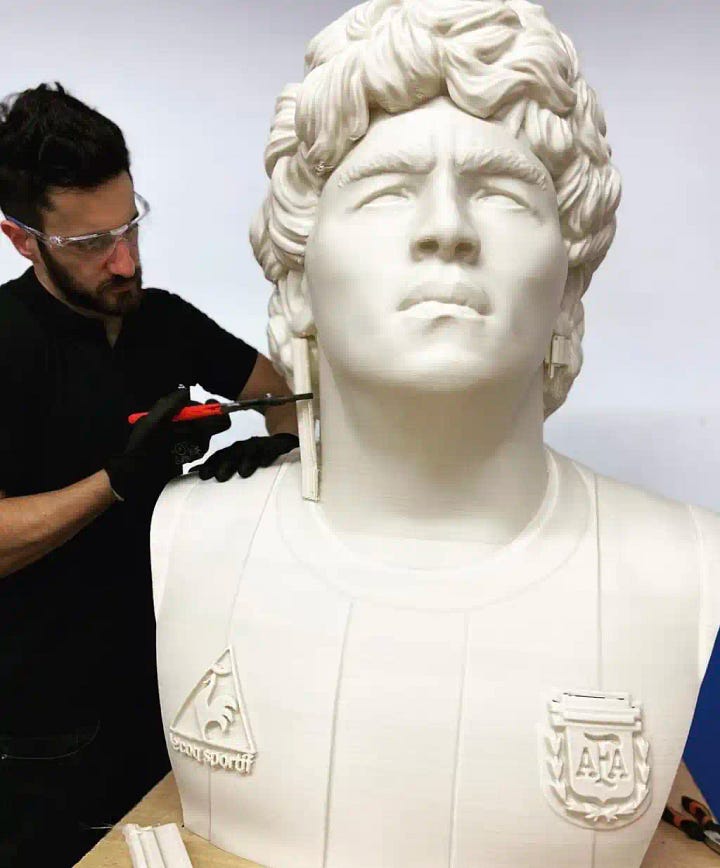
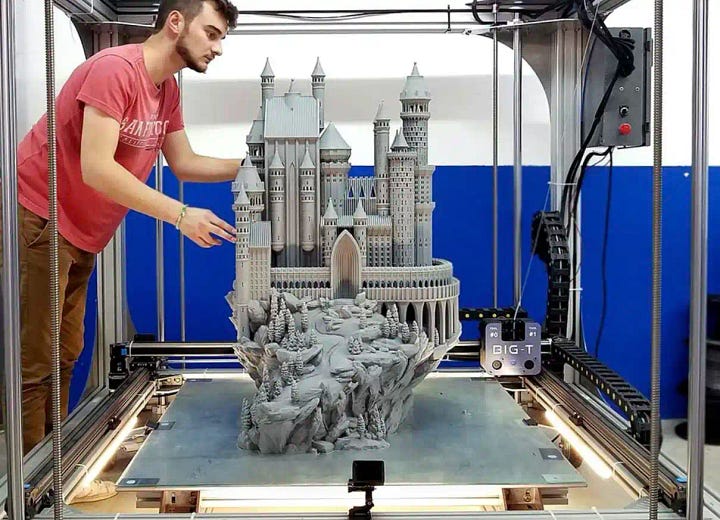
Trideo
Remedios de Escalada de San Martín 3749, CABA - 1407, Argentina
Monteiro de Melo 667, 05050-000 SP, Brasil
Rafael Delgado 97, Obrera, Cuauhtémoc, 06800 Ciudad de México, CDMX, Mexico.
Founded: 2014
www: trideo3d.com
e-mail: laurent@trideo3d.com
social media: LinkedIn | Facebook | Instagram | YouTube
Business activities: Hardware Manufacturer and AM Service Provider
AM Services:
FDM / FFF
SLA / DLP
Distribution:
Trideo – Big T
Trideo – Dual T-500
Trideo – Dual T-300
Trideo – T600
Activity: South America
Overview:
Trideo 3D is a leading 3D printing company with operations across Argentina, Brazil, and Mexico, dedicated to empowering professionals and businesses through cutting-edge additive manufacturing solutions.
Founded in 2014, Trideo specializes in advanced 3D printing solutions, catering to diverse professional needs. The company designs and manufactures 3D printers capable of producing large-scale parts (up to 1m³) and working with high-performance engineering materials such as ULTEM, PA, PC, ASA, and carbon fiber composites.
Trideo also offers comprehensive 3D Printing Services, delivering solutions for large production volumes, intricate designs with express delivery time.
Legacy:
Present in three countries across Latin America, Trideo provides a consistent standard of quality, making us a trusted partner for large companies with international projects.
Trideo’s dual expertise in manufacturing 3D printers and offering professional 3D printing services ensures clients benefit fully from our knowledge and experience, even for their most challenging needs.
With additional services in 3D design and consulting, Trideo stands out as one of the most complete 3D printing companies in Latin America.
YIZUMI
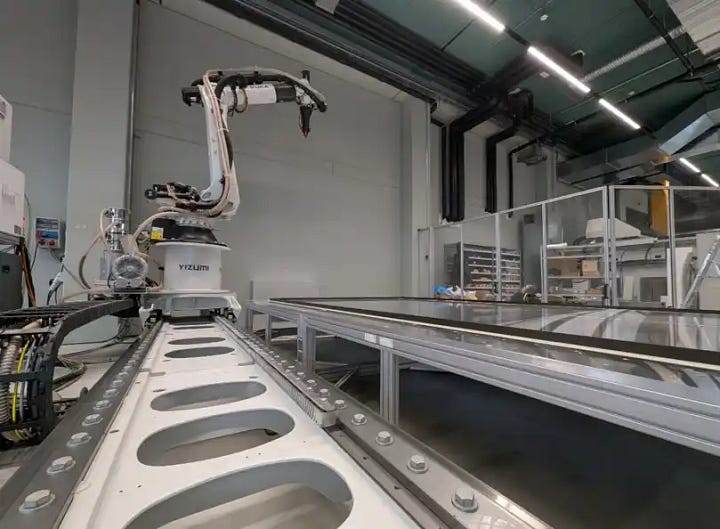
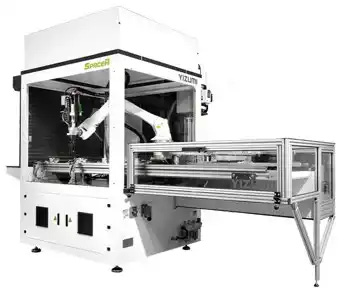
YIZUMI Germany GmbH
Konrad-Zuse-Straße 41, D 52477 Alsdorf, Germany
Founded: 2017
www: yizumi-germany.de
e-mail: info@yizumi-germany.de
social media: LinkedIn | YouTube
Business activities: Hardware Manufacturer
Distribution:
SpaceA S-Line
SpaceA B-Line
SpaceA E-Line
SpaceA C-Line
Activity: World
Overview:
YIZUMI (www.yizumi.com), a Chinese machine manufacturer with over 4,000 employees, produces and offers automated solutions in the areas of injection molding, die casting, rubber injection molding, thixomolding and 3D printing, making it the only machine manufacturer in the world to cover all areas of high-pressure injection molding. In terms of production volume, the company ranks second in the world.
Legacy:
Yizumi Germany GmbH is the German development and sales company of Yizumi Precision Injection Molding and Die Casting AG. The Yizumi Germany GmbH is located in the Alsdorf industrial park in the Aachen area and is the innovation center of the Yizumi Group, which is focused on pre-developments.
The Yizumi developers do not only deal with the optimization of the machine technology, but also with the process development. Thus, the focus is on offering the customer innovative and smart process solutions, which above all offer a cost advantage in the form of final component costs.
In addition, Yizumi Germany offers you sales opportunities in the entire Yizumi product portfolio.
ZIKNES
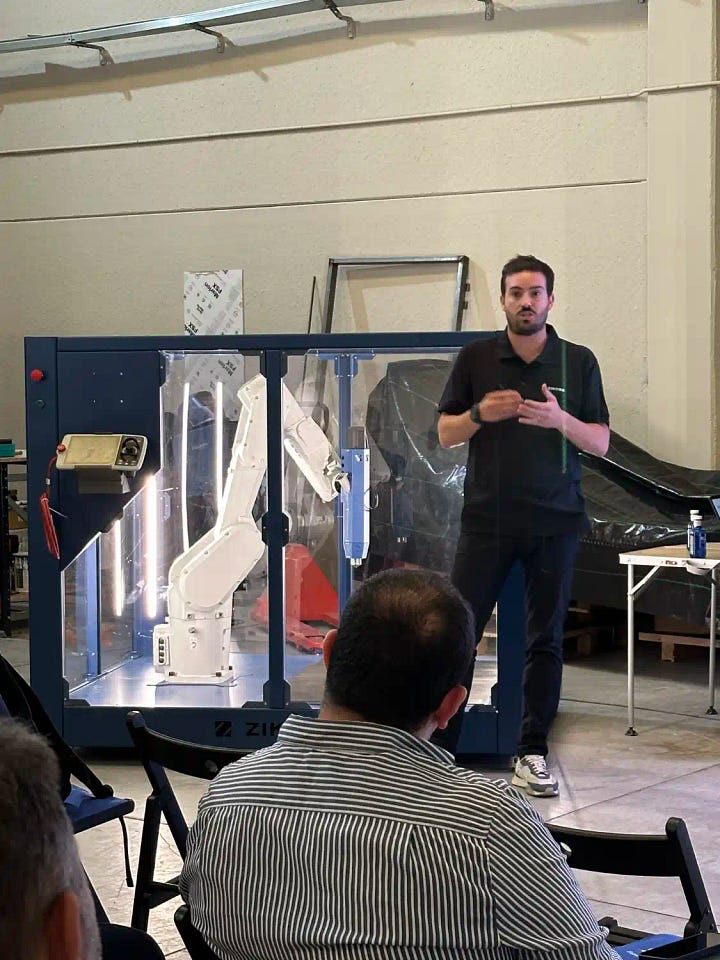
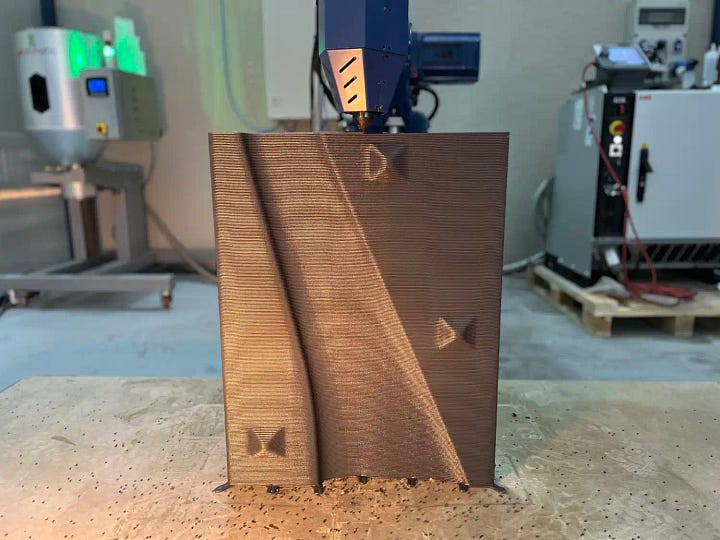
Ziknes
Calle manel tomas 12Bm, 46110 Godella, Valencia, Spain
Founded: 2021
www: ziknes.com | laminar3d.com
e-mail: contact@ziknes.com
social media: LinkedIn (Ziknes) | LinkdIn (Laminar 3D)
Business activities: Hardware Manufacturer and Software Developer
Activity: World
Overview:
Ziknes is a leading company in Large Format Additive Manufacturing (LFAM), providing fully integrated 3D printing solutions for industrial-scale production. Its portfolio includes:
Z.Pellet: high-performance robotic arm-based 3D printer designed for large-format manufacturing.
Z.Kompact: compact, mobile robotic printer ideal for research centers, universities, and industrial applications with space constraints.
Z.Conversion: conversion package that transforms existing industrial robots into high-efficiency 3D printing systems.
Ziknes technology supports a wide range of thermoplastics, including composites and custom-engineered recycled materials, enabling high-performance and sustainable manufacturing.
At the core of its ecosystem is Laminar, a proprietary software suite that integrates slicing and process control, ensuring precision, automation, and seamless integration with robotic 3D printing. This combination provides an end-to-end solution for prototyping, mold production, and final part manufacturing.
Beyond technology, Ziknes is committed to helping companies transition to robotic 3D printing by providing training, expertise, and tailored solutions to seamlessly integrate LFAM into their existing production workflows.
For engineers, by engineers.
Legacy:
Founded in Spain, Ziknes was created with a global vision: to revolutionize large-scale 3D printing through advanced robotics, hardware, and software. With a multidisciplinary team of engineers and designers, the company seamlessly integrates automation and additive manufacturing, driving innovation in industrial production.
In 2024, Ziknes secured a €1 million investment round to fuel its international expansion in 2025, with a strong focus on Europe, the U.S., and Asia. This funding enables the company to scale its global reseller network, establish strategic partnerships, and accelerate the adoption of LFAM across multiple industries, reinforcing its position as a leader in robotic additive manufacturing.