Atomic Layer of the Day:
Today I came across a short video of a 3D-printed shoe sole made from TPU on the new Bambu Lab H2D 3D printer. The video was created by Phil Tsao, a fairly well-known figure in the 3D printing community on X, and the owner of Ember Prototypes.
Phil manufactures, among other things, custom PEI build plates for popular FFF-type 3D printers.
Ring a bell? If not yet, it’s definitely worth following Phil on X — he does some really cool stuff with 3D printers. Like this sole, for example:
(Unfortunately, I can’t embed X posts on Substack, so you’ll have to click the image to watch the video.)
The print was made using Polymaker 3D’s TPU 95A HF. The supports were printed from random PLA.
So what makes it so remarkable?
Well, in principle — nothing. It's just a 3D print like many others. We’ve seen this before.
But the thing is, for many new 3D printer users, this is now the standard. For old dogs like me, it’s still something amazing.
You see, just 7–8 years ago, successfully printing anything with TPU was considered an achievement — and geometries like this one, in that orientation, were completely out of the question. Meaning the print simply wouldn’t come out right.
Back then, TPU had to be printed very slowly and flat — so that the largest possible surface of the model would be in contact with the build plate. Of course, that approach had its own big issues, especially in terms of aesthetics (with large, visible top-layer lines), and when using supports, they would leave really ugly marks — since supports were also made from TPU.
Today, we can position the model at almost any angle without worrying about supports — which can now be printed from another material (ideally PLA). This became possible thanks to two breakthrough features. Originally created to generally improve 3D printer workflows, they turned out to be revolutionary specifically for TPU.
The first one is “tree” or “organic” supports. Ultimaker was the first to introduce tree-style supports as an experimental feature in Cura version 3.2.0, released in February 2018. These supports were developed by Thomas Rahm and officially integrated into Cura 4.7.0 in 2020.
Then, PrusaSlicer introduced its own version, called “Organic Supports,” in version 2.6, released in 2023. Around the same time, they also appeared in Bambu Studio.
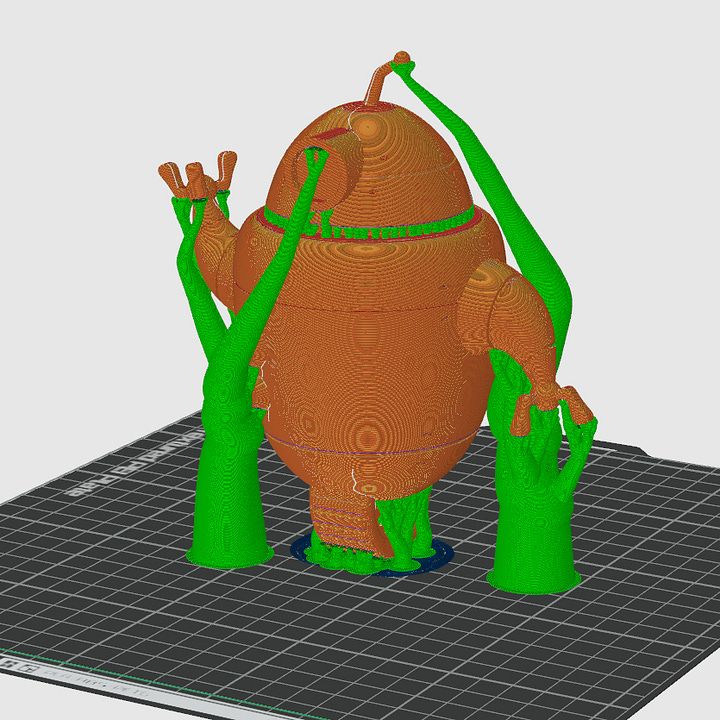
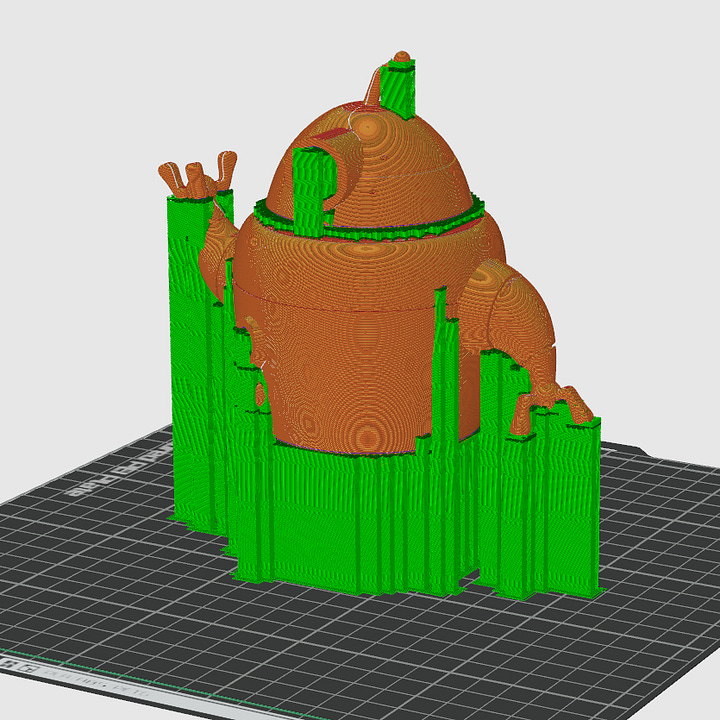
Over time, tree & organic supports completely revolutionized FFF 3D printing, enabling the creation of geometries that had previously been limited by the first rule of 3D print orientation: maximize the surface area touching the build plate.
Once these supports came along, that rule no longer applied. Models could be suspended in mid-air, completely changing the logic behind their design.
The second breakthrough is filament-changing systems — MMU and AMS — popularized by Prusa Research and Bambu Lab. Originally designed mainly for color changes and multicolor printing, they eventually began to be used to create supports from a different material than the model itself — a game-changer for TPU in particular.
And although the model in the video was printed on a dual-head Bambu Lab H2D, the concept of using PLA-based supports for TPU originated from experiments with MMU and AMS on single-extruder 3D printers.
At the same time, I still believe that working with elastomers on desktop-grade FFF 3D printers is really only just beginning. These materials, due to their high difficulty of processing on older-generation printers, were rarely used — and their application areas were very limited.
That’s now starting to change.
Atomic Layer from the Past:
04-19-2016: Formlabs introduced Dental SG – the first biocompatible resin designed for desktop 3D printers.
News & Gossip:
Helio Additive integrated its cloud-based Dragon simulation into OrcaSlicer, enabling voxel-based print analysis for FFF users at no cost. The tool predicts thermal/mechanical behavior, flagging issues like warping or poor adhesion in under a minute. Users input printer, material, and ambient temps for precise results. Free for basic use; paid upgrades offer advanced optimization. Supports 45+ materials, expanding to 250 by year-end.
4WEB Medical has surpassed 100,000 spine procedures using its FDA-cleared 3D-printed TRUSS Implant Technology. The patented lattice design enhances structural performance and promotes bone growth.
Pratt & Whitney is implementing metal DED additive manufacturing to accelerate GTF engine component repairs, cutting process time by 60% and saving $100M in parts recovery over five years. The Florida-developed method reduces tooling costs and material dependencies. The company plans to scale this technology across its global MRO network, with potential for wider engine component restoration.